Hydroponic crops like basil often taste better than soil-grown plants as the optimal specific nutrients supplied to the plant maximise quality and aromas. Hydroponic production boosts growth far beyond what can be achieved from growing in traditional soil based field culture methods, and uses far less water. The water is continually being recycled and thus nutrients are not lost and are entirely utilised by the plant. Growing hydroponically can be productive on any scale from home to multi-hectare intensive greenhouse facilities.

Basil is one of the most popular herbs available today and is a particular favourite for both home cooking and professional chefs, and used in an incredibly extensive range of commercial food products. Basil belongs to the mint family (Lamiaceae) and is very easy to grow commercially. A popular choice to commence with when starting off in commercial hydroponics, basil is available in a variety of types. The common ones being Thai, Purple, Lemon, Lime, Spicy and Sweet basil which has the larger more succulent leaves.
Hydroponic basil production has almost none of the dilemmas that are encountered with soil-grown basil. Commercial hydroponic enterprises commonly utilise the more common Nutrient Film Technique (NFT), and is ideally housed within purpose built green-house growing facilities. This agricultural method does not entirely need to be excluded from the outside environment.

Commercial hydroponic production produces basil in a very short time frame, sometimes to marketable size in about thirty days. This allows fast turn-over and constant regular supplies to the numerous available markets. Hydroponic basil production is one perfect example of where an ancillary agricultural enterprise creates diversification value with aquaculture. AusAquaTec have done trials utilising commercial aquaculture pond water to grow hydroponic crops, requiring very little additional fertilising elements, with very promising results.

Most current hydroponic farms rely on natural sunlight to generate growth. Basil prefers warmer temperatures of over 20 degrees Celsius and under 30 degrees Celsius, with a commercial optimum in the higher twenties for faster growth. Hence, growing in commercial green-houses allows greater environmental control and faster turn-around. It grows best in less than 70% humidity and low condensation, and like most hydroponic cropping, necessitates good air flow.
Basil is ideally spaced about 15cm apart and requires only a 40 to 50mm pot. The hydroponic channel size preferably needs to be approximately 100 to 140 millimetres wide and and 70 to 80 millimetres deep. Many hydroponic farms use PVC channels and plumbing, and even though may be UV protected, this plastic type is known to leach harmful chemicals. Leached chemicals from PVC may then be absorbed into the crop for human consumption.

All forms of food production necessitates the need to utilise food grade production methods and equipment. To assist achieve contaminant free production, channels, plumbing and water holding/storage tanks need to be made from food grade plastics, predominantly polypropylene (PP) and/or polyethylene (PE). Using these plastics in production and packaging is increasingly demanded upon by regulators and markets, and a prerequisite for organic production.
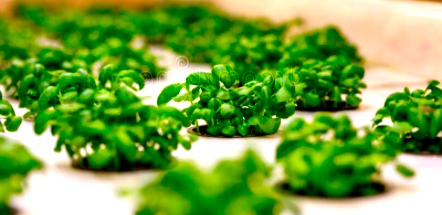
Basil is commercially grown from either seeds or cuttings, however seeding is generally the preferred method for hydroponic production. The seeds are germinated in a grow media such as a combination of equal parts coconut peat and vermiculite, or specific hydroponic ‘starter plugs’. We are endeavouring to research a more sustainable and cost effective techniques than these current traditionally used grow medium methods.
Basil seeds are quite small and swell slightly when soaked in water to form a gelatinous covering. Germination more efficiently occurs at the optimal temperature of 25 to 27 degrees Celsius over 5 to 7 days. The seeds must not be over saturated as the seed is susceptible to rot, therefore the grow media must be well drained.

Too much watering during and after germination can easily generate fungal disease. A mild nutrient mix is applied to the seedling when the leaves start to grow, nominally with an Electroconductivity (EC) of 0.5m mScm-1 and a pH 5.8 to 6.2. Seedlings need to be a height of about 40 to 70mm before transplanting into the hydroponic system.

To maximise production, basil need a minimum of 14 hours of light per day, with high light levels of a minimum Daily Light integral (DLI) of 12 mol per metre square. A growing crop may require a specific supplemental LED lighting (spectral) formula during winter with this less daylight hours.
Temperature control is achieved by adjusting the green-house environmental controls, such as raising or lowering side walls, and/or opening or closing roof vents. Temperature stabilisation can be maintained by incorporating below-ground water transfer plumbing and storage which creates thermal insulation. As is the case with many hydroponic crops, basil needs a higher nutrient electrical conductivity (EC) in winter than summer, but usually around 1.4 to 2.0mS for maximised growth.

Nutrient solution is basically one specific to herbs and leafy greens, but as always with hydroponics, the specific nutrient solution depends on the water source and quality. Therefore, testing the intended water source at the preliminary commercial planning feasibility stage is imperative. Underground bore water is often the preferred source for both aquaculture and hydroponics, often being the most purest water supply. Some bore water sources can be too high in iron, but this can be treated.

The basic nutrients required are nitrogen for leaf yield, potassium and calcium (usually supplied in equal amounts) which help with plant oils and flavour, and magnesium (at for example 50ppm concentration) to help yield essential oils and aroma. As always, hydroponic nutrient formulas necessitate a specific extensive list of ingredients of macro and micro nutrients for any intended crop to maximise growth and quality.
Most commercial hydroponic farms purchase nutrients in powder from, and mixed in purpose designed nutrient tanks to form a specific liquid formula, which is then fed to the main recirculating storage tank system. Nutrient water is then pumped to the hydroponic grow channels to feed the crop, and then gravity drained back to the main storage tanks. Mechanisation and hydroponic technologies, such as automatic ‘dosers’, are very much simplifying production methods.
Basil, like so many hydroponic crops, are susceptible to fungal and mould pathogens such as downy mildew. Proper production methods and hygiene techniques will significantly eliminate threats from fungal and mould diseases. This is absolutely imperative in commercial hydroponic production as a facilities entire crop may need to be destroyed to control and eliminate such threats.


Contingency plans, established at the early planning stages, will help reduce financial impacts and disruption to market supply. Prophylactic and eradicative organic treatments are also effective in significantly negating fungal and disease outbreaks. Neem oil application is one very effective organic treatment.
Basil, also like so many hydroponic crops, are susceptible to many pest insects like aphids, thrips, whiteflies, mites, caterpillars and grasshoppers. Such pests can very much enjoy devouring the hydroponic produce, causing plant damage and hence reduced yield and quality. A very powerful approach to combating such pests in common commercial hydroponic production is the Integrated Pest Management (IPM) method.


One aspect of the IPM method is the introduction of predator insect species to control the insect pests that damage crops. Commercially available predator insects include ladybirds, wasps, killer mites and praying mantis. IPM strategies will become more necessary with increasing resistance to chemicals such as pesticides. Pest controlling chemical also have damaging compounding and long lasting detrimental effects on all of our vital ecosystems. Markets are also demanding that more agricultural production be pesticide and fungicide free.
Of course another more increasingly developed approach to hydroponic food supply is production in the more industrial factory style facilities, with total environmental control and total exclusion from the natural environment. These facilities can be located within urban centres, however the use of municipal water requires filtration to remove harmful chlorine and fluoride.

Lessons can also be learnt from broad-acre cropping, now using targeted pest control based on information collected from remote sensing, as apposed to total chemical coverage. Another advantage of hydroponic production, with it’s intensive scale in a relatively small space, is that observation and monitoring of crop health is significantly far simpler.

Basil will be affected in hydroponics, as with many other hydroponic crops, if the water nutrient supply is interrupted for any length of time. This is usually caused by power interruptions or plumbing failures. Plants do however often recover quickly if the interruption is not lengthy. This threat does display one of the very few weaknesses of the NFT production method, and is usually always negated with effective planning, facility design and monitoring.
Contingency planning is imperative with any agricultural enterprise and a clear understanding of the threats and weaknesses must be acknowledged and addressed at the initial planning stage. So that when something does goes wrong, and it invariably will, methods and techniques are already in place for immediate implementation.
Growing basil with other crops depends on compatibility of the optimised growing conditions. Pruning basil can be an option to create a more bushier plant with greater volume, but is often not financially justified due to the crops ability for rapid growth. Harvesting is extremely easy in hydroponics, and the final product is packaged and delivered in plastic conical wrapping with an open base.

To maintain freshness, the final harvested product is delivered to the end user as soon as possible. The produce is stored and transported chilled, at around 10 degrees Celsius, and once delivered to the end user can easily be stored in a container of water to maintain shelf life.

A significant advantage of hydroponic production, due to the production method requiring far less space and water than soil-based cultivation, is therefore the ability to situate these efficient food production enterprises closer to the desired markets. This significantly reduces the often expensive transport costs associated with many agricultural industries, and allows the produce to be supplied with greater freshness. Hydroponic production and demand is expanding world-wide, and by necessity, is one of the more critical commodities of the future.


